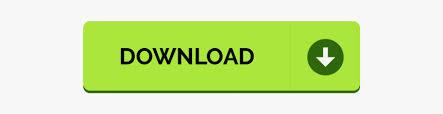
This textbook has been written wi.ĬADCIM Technologies, 525 St. In this textbook, the author has adopted a tutorial-based approach to explain the fundamental concepts of SolidWorks. SolidWorks 2012: A Tutorial Approach introduces readers to SolidWorks 2012 software, one of the world's leading parametric solid modeling packages. SolidWorks 2012: A Tutorial Approach (ISBN: 978-1-93) In this book, the author has adopted a tutorial-based approach to explain the fundamental concepts of SolidWorks. SolidWorks 2014: A Tutorial Approach book introduces readers to SolidWorks 2014 software, one of the world's leading parametric solid modeling packages. SolidWorks 2014: A Tutorial Approach (ISBN: 978-1-93) In this textbook, the author has adopted a tutorial-based approach to explain the fundamental concepts of SOLIDWORKS. SOLIDWORKS 2016: A Tutorial Approach introduces readers to SOLIDWORKS 2016 software, one of the world's leading parametric solid modeling packages. SOLIDWORKS 2016: A Tutorial Approach, 3rd Edition (ISBN: 978-1-94) SOLIDWORKS 2018: A Tutorial Approach introduces readers to SOLIDWORKS 2018 software, one of the world's leading parametric solid modeling packages. SOLIDWORKS 2020: A Tutorial Approach introduces readers to SOLIDWORKS 2020 software, one of the world's leading parametric solid modeling packages. This video shows the set up and running of a thermal simulation that looks at the temperature distribution occurring on a brake rotor while stopping. Check out more Simulation information and training options at CATI.SOLIDWORKS 2020: A Tutorial Approach, 5th Edition (ISBN: 978-1-64057-102-0) 0 Check out this video tutorial using SolidWorks Simulation to run a FEA thermal analysis on a brake rotor from the SolidWorks SAE tutorial. No matter what type of analysis you choose to perform these same six steps will guide you from start to finish. Steps 1-4 are pre-processing, and steps 5-6 are post-processing. Stress, Displacement, Strain, Factory of Safety are among the most common, however, SOLIDWORKS Simulation provides a wide range of result options. The sixth and final step is to review the results. Running or solving the analysis can be done individually or in batch mode if multiple studies need to be solved. The fifth step is where the computer does the heavy lifting. SOLIDWORKS offers a host of mesh options including Solid, Shell, and Beam mesh types. The fourth step is to discretize or mesh the model. This is the most important step in the process and consists of assigning Loads, Fixtures, Contacts, and Connectors. SolidWorks Premium 2012 gives you powerful, easy-to-use functionality that increases your productivity and empowers innovative design.It automates the tasks you use most often and allows you to streamline your product development workflow.
SOLIDWORKS 2012 SIMULATION TUTORIAL FREE
The third step is the Free Body Diagram step and tells Simulation how the model behaves in the real world. These SOLIDWORKS tutorials cover fundamental and advanced functions of SOLIDWORKS. The mechanical properties required to solve the specific analysis type are highlighted in red. Learn SOLIDWORKS and create 3D CAD models for engineering, sheet metal design, product design, and other projects. The material database is the same as the SOLIDWORKS material library so the material can carry over from the SOLIDWORKS model. Step two can be done by a right mouse button on the part or by selecting the material from the command manager. Once the study type has been chosen the Simulation Feature Tree opens below the SOLIDWORKS feature manager tree. In this example below a Static Study is specified. Left to right on the command manager, or top-down in the Simulation feature tree these six steps are visible.įirst, choose New Study and pick the study type that applies to your analysis needs. Step 3: Apply the Boundary Conditions (Free Body Diagram) Part of SOLIDWORKS Simulation’s ease of use are the simple Six Steps that every Simulation Study shares. SOLIDWORKS Simulation used to be called COSMOS Works, and since its early days, the Finite Element Analysis program has strived to be powerful, accurate, and EASY to use. SOLIDWORKS Simulation has been around for years tracing its roots back to 1982 and the Structural Research and Analysis Corporation (SRAC).
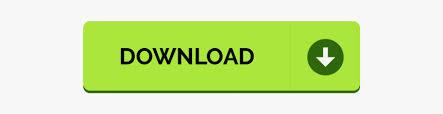